Students
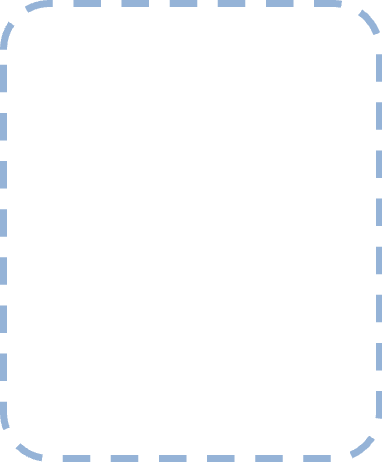
Jerome, Masters, KU Leuven (BE)
Diamond is the most robust thermomechanical material, making it a natural candidate for fusion applications. 3D printing of complex shapes from low-cost diamond powder will be studied.

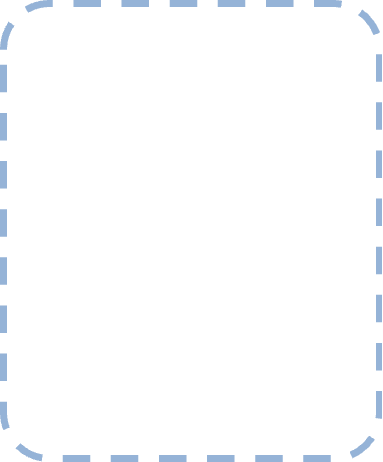
Claudia, Masters (2 year), University of Derby (UK)
Laser-DPF life cycle assessment for sustainability and social responsibility. Understanding the impacts of a future industrial supply chain is a key input to the commercialization process.

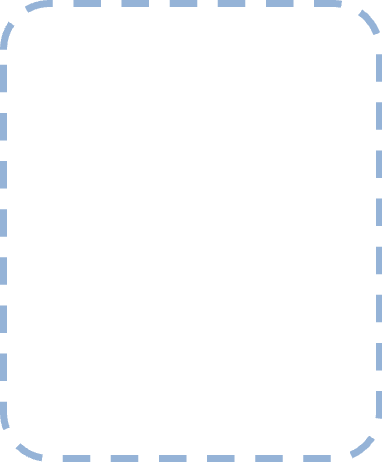
Ahmed, PhD, University of Manchester (UK)
The fusion fuel operates at millions of degrees, damaging everything inside the reaction chamber. Options for high-performance 3D printed refractory metal components will be evaluated.

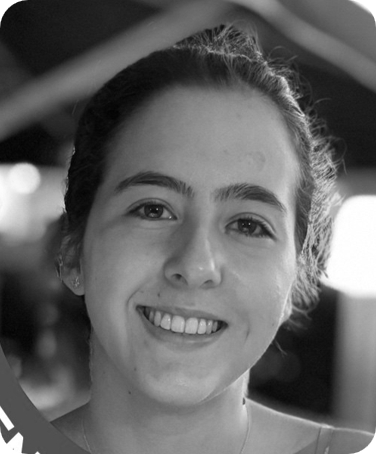
Carys, undergraduate project, U. Manchester
3D printed parts for fusion will need post-processing. Tungsten samples were characterized in the lab and surface finishing methodologies reviewed (here).

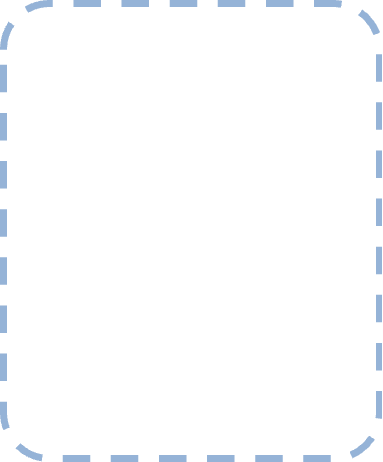
Asif, undergraduate project, U. Manchester
As indicated above, 3D printing is central to the materials effort. A survey of commercial refractory metal advanced manufacturing suppliers was conducted.

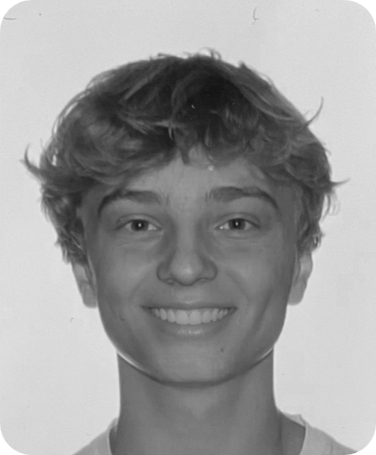
Jaan, undergraduate project, KU Leuven
If net energy is produced by the laser-DPF, output will be limited by the thermal engineering of the electrodes. Heat transport calculations were made to guide operation.

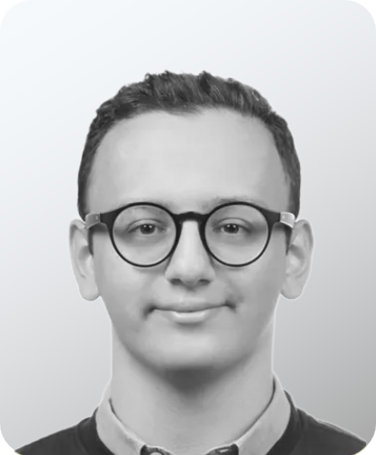
Ă–mer, Masters, KU Leuven
Sufficient electrode lifetime is a challenge for a commercial DPF system. Liquid metal surfaces are being evaluated, which are interesting to several fusion concepts.

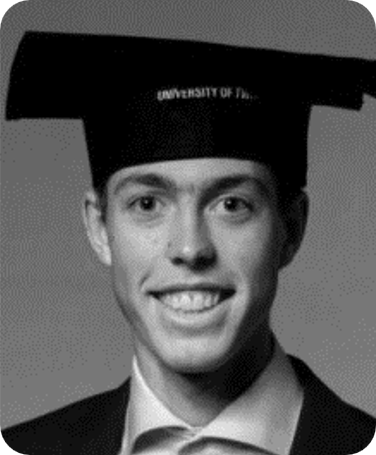
Joris, Masters, Eindhoven University of Technology, TU/e (NL), graduated with distinction
A commercial DPF needs to pulse steadily, like the cylinders of a gasoline car engine. To satisfy this requirement, configurations of solid-state high-voltage electronics were tested.
